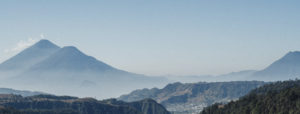
Successful completion of one of our projects in Guatemala
Successful completion of one of our projects in Guatemala Laura Núñez Muñoz More than 20 years of general experience and, for the last 15 years,
In all companies there are misalignments that go unnoticed and reduce efficiency. Among the different departments that can be identified in a company, this article will focus specifically on the production area, where mismatches such as unnecessary movements, waiting times, defects, etc. can occur, leading to economic losses in the manufacturing processes and, as a consequence, reducing their value.
In order to obtain cost reduction and add value to the different processes, there are different methodologies. Among them is the “Lean Manufacturing” philosophy, which seeks continuous improvement, trying to eliminate or reduce activities that do not add value, which it calls “muda”, and dominate those with added value.
This philosophy, applicable to any type of process, was born in Japan in the 1950s by Taiichi Ohno. During the Second World War, Ohno began working at the Toyota Motor Company, where he became director in 1954. It was at this automotive company that he began to realise the wastefulness that was taking place, which was driving up production costs as a result. His main principle is the “Just In Time” philosophy, aimed at putting only the necessary products or services on the market, in the right quantity, with the required quality, at the right time and at the lowest cost, with the objective of harmonising production and demand.
The first thing to be done is a diagnosis of the current situation, the main task being the identification of unnecessary costs throughout the production process. This philosophy identifies a total of 7 mudas:
The identification of mudas must be accompanied by the quantification of data, indicators, information and the establishment of quantifiable objectives. In order to do this, it is necessary to know what is happening, which is why control must be carried out by establishing data collection mechanisms.
In short, by identifying mudas and implementing different methodologies to prevent their occurrence, a significant reduction in costs can be achieved. However, it is not enough to apply this philosophy sporadically or when a failure is detected; it must become a habit. Moreover, it is a company philosophy, and therefore requires the coordination of the activities of all areas/departments for it to work properly.
At Euro-Funding we work by identifying opportunities and elaborating proposals for productive improvements, adding value throughout the entire life cycle of purchasing and procurement. Thanks to the methodology we use during the project management process, we manage to increase the market share and profitability of our clients.
Successful completion of one of our projects in Guatemala Laura Núñez Muñoz More than 20 years of general experience and, for the last 15 years,
PERTE for industrial decarbonisation approved PERTE for industrial decarbonisation approved The PERTE is approved with the aim of accompanying industry in its decarbonisation process to
Keys to efficient driving Enrique Roca Industrial Technical Engineer with specialization in Mechanics. He is currently Technical Manager in the Energy Efficiency and Sustainability unit